Zement, Kalk und Papier
Unsere Lösung für die Zement-, Kalk- und Papierindustrie
Die Kalzinierung von Calciumcarbonaten und deren anschließende thermische Verarbeitung spielen in zahlreichen Branchen eine Schlüsselrolle – insbesondere im Bauwesen und in der chemischen Industrie.
Zementklinker und gebrannter Kalk sind Grundbestandteile von Baustoffen. Gebrannter Kalk findet darüber hinaus breite Anwendung in Industrieprozessen wie Zellstoff-, Soda- oder Zuckerherstellung. Heute steht die Produktion unter dem Druck von Effizienzsteigerung und Nachhaltigkeitsanforderungen. CO₂-Emissionen aus Rohstoffen beeinflussen maßgeblich die Wirtschaftlichkeit der Kalzinierung. Daher ist Effizienz in jeder Phase entscheidend. Störungsfreie Produktionskampagnen, minimale Stillstandzeiten und thermisch effiziente Auskleidungen von Drehrohr- oder Schachtöfen bieten einen klaren Wettbewerbsvorteil. Unsere Mission bei PCO ist es, unsere Partner mit feuerfesttechnischen Lösungen für Kalk- und Zementöfen zu unterstützen – von der ingenieurtechnischen Planung über die gemeinsame Auswahl optimaler Materialien und Montagemethoden bis hin zu Logistik weltweit sowie fachgerechter Montage und Überwachung. Die bewährte Qualität unserer Produkte und Dienstleistungen, verbunden mit umfassender Betreuung, minimiert Produktionsausfälle und hilft unseren Kunden, wettbewerbsfähiger und nachhaltiger zu werden.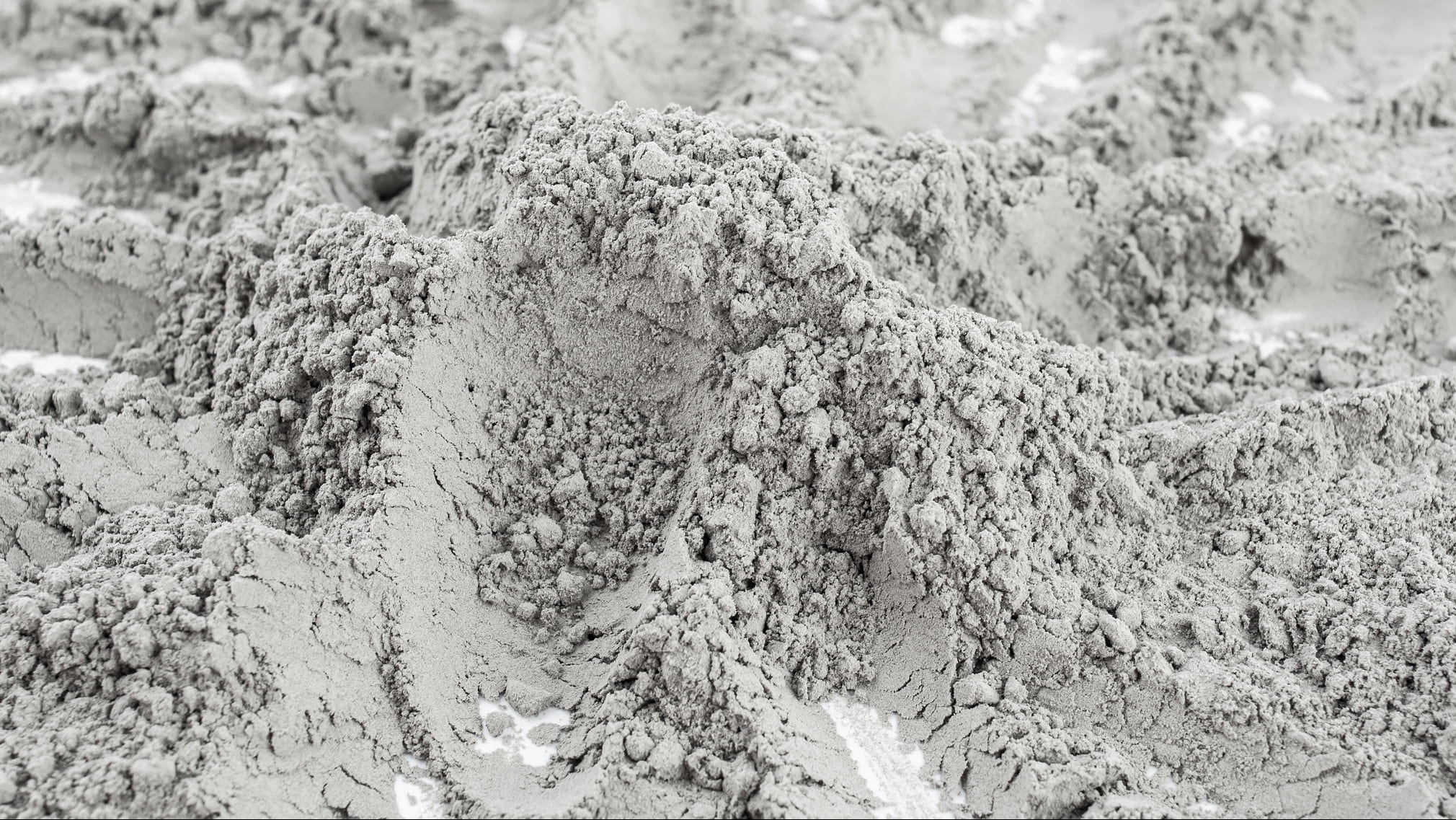
Was wir für Sie tun können
Wir entwickeln
- Auswahl geeigneter feuerfester Werkstoffe entsprechend den Bedingungen des Produktionsprozesses
- Optimale Konfiguration der Feuerfest-Auskleidung unter Berücksichtigung von Anlagentyp, Prozesszonen, Betriebsbedingungen und Kundenpräferenzen
- Thermische Strömungsanalysen für verschiedene Auskleidungsvarianten (A/B-Vergleiche)
- Optimierung der Auskleidungskonstruktion zur Erhöhung der Standzeit und Reduktion von Wärmeverlusten
Wir produzieren und liefern
- Schamott- und Hochaluminaprodukte mit erhöhter Abriebfestigkeit – geeignet für Wärmetauschertürme, Tertiärluftkanäle, Kalzinatoren, Steigrohre in Zementanlagen sowie kühlere Ein- und Austrittszonen in Kalköfen
- Innovative niederzement- und zementfreie Betone für vielfältige Anwendungen in Zementanlagen, angereichert mit SiC- oder ZrO₂-Zusätzen
- Dämmprodukte für Schutzschichten in Schacht- und Drehrohröfen, einschließlich Qualitäten mit erhöhter mechanischer Festigkeit
- Vorgefertigte Elemente, montagefertig, ohne notwendige Aufheizvorgaben
Wir montieren
- Demontage und Montage von Feuerfest-Auskleidungen in allen Anlagenteilen von Zementwerken sowie in Schacht- und Mehrschachtöfen
- Entsorgung demontierter Feuerfestkeramiken (Ofenbruch)
- Laufende Reparaturen und Notfallinstandsetzungen während Wartungskampagnen
- Technische Beratung – Ursachenanalyse von Verschleiß, Standzeitoptimierung und Überwachung der Ofenauskleidung
Öfen und Hochtemperatur-Industrieanlagen
Obere Zyklone
Die oberen Zyklonstufen spielen eine wesentliche Rolle bei der Zementklinkerproduktion – sie gewährleisten die Durchmischung, den Transport und die Verteilung der Rohstoffe. In dieser Zone wird das Material schrittweise auf bis zu 600 °C erhitzt. Der kontinuierliche Betrieb stellt hohe Anforderungen an die Feuerfestmaterialien hinsichtlich Abriebfestigkeit. Ein Zyklon wird feuerfesttechnisch in drei Hauptzonen unterteilt: Gewölbe, Zylinder und Konus. Die Hauptbelastung entsteht durch Abrasion durch das strömende Schüttgut; die Temperatur spielt eine geringere Rolle. Da obere Zyklone nur in sehr langen Abständen gewartet werden (mehrere Jahrzehnte), ist der Einsatz besonders langlebiger Materialien entscheidend. PCO bietet maßgeschneiderte feuerfeste Lösungen: In Standardbereichen kommen Schamottsteine der NORMATON-Serie zum Einsatz, bei stärkerer Abrasion empfehlen wir EXTRATON-Produkte. In speziellen Fällen können auch Beton-Auskleidungen verwendet werden, um zusätzliche Stabilität zu gewährleisten.
Angebotsumfang: Futterdesign Lieferung von feuerfesten Produkten Dienstleistungen im Bereich Auskleidungsinstallation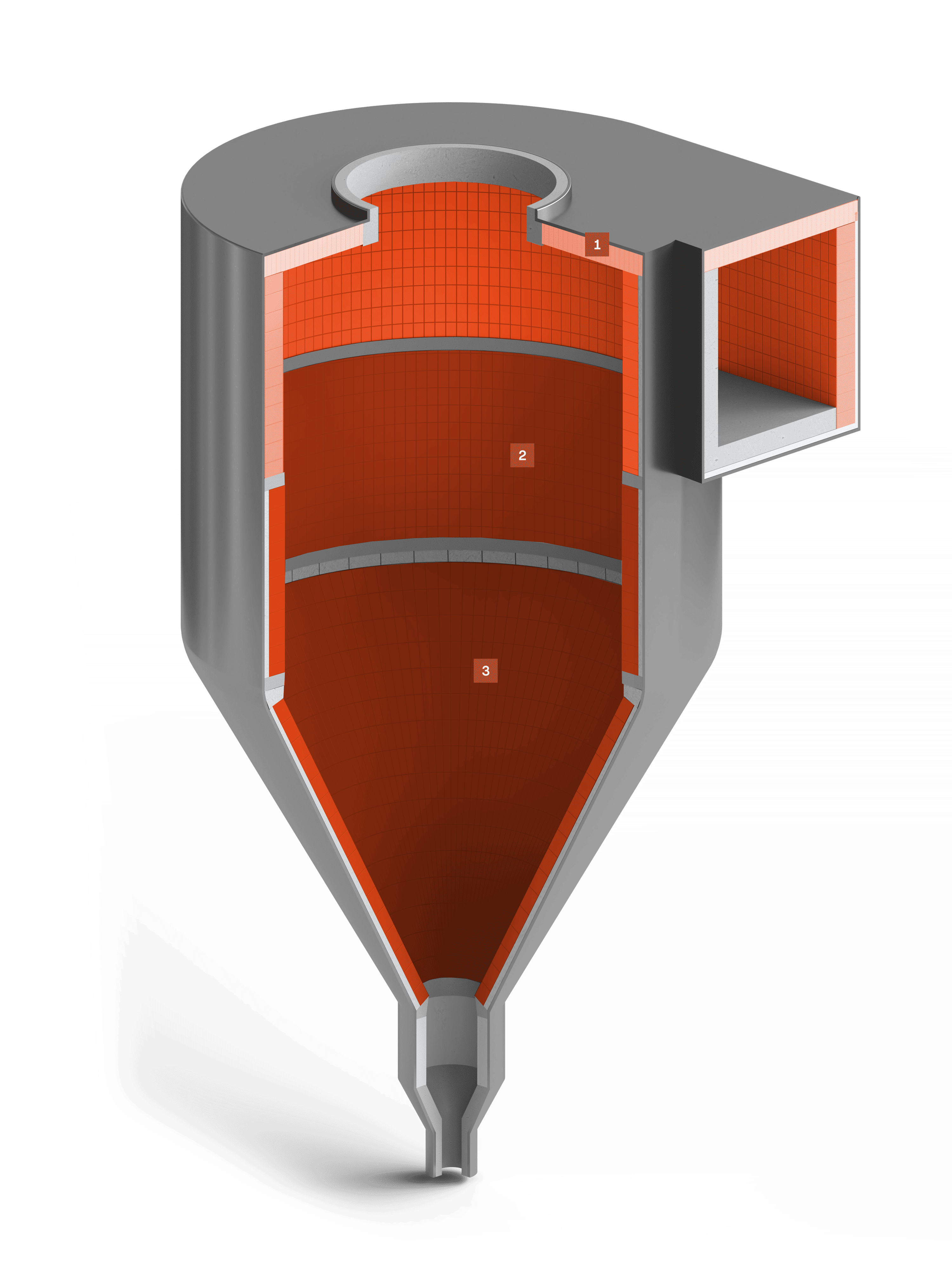
Das Gewölbe ist hauptsächlich gasgetragenem Abrieb durch flüchtige Partikel des Rohmaterials ausgesetzt. Die Temperatur- und mechanische Belastung ist gering, weshalb die Betriebsbedingungen als moderat gelten. Das Gewölbe wird mehrschichtig ausgekleidet – insbesondere mit Keilsteinen für Arbeits- und Dämmschichten. Ideal geeignet sind niedrigaluminahaltige EXTRATON-Steine sowie leichte ISOLUX-Dämmprodukte, die Abriebfestigkeit mit guter Isolierleistung kombinieren.
Auch im Zylinder des oberen Zyklons wirken mechanische und abrasive Belastungen, jedoch in moderatem Maße. Die mehrlagige Auskleidung – erneut mit Keilsteinen – gewährleistet gleichmäßige Lastverteilung und langlebigen Schutz. Die gleichen Materialien wie im Gewölbe kommen zum Einsatz: EXTRATON für Abriebfestigkeit, ISOLUX für Wärmedämmung.
Der Konus ist der mechanisch am stärksten belastete Teil, allerdings bleibt das Gesamtrisiko für das Mauerwerk relativ niedrig. Aufgrund seiner komplexen Geometrie wird hier bevorzugt Beton eingesetzt, da er sich besser anpasst und gleichmäßig aufgetragen werden kann. Ziel ist eine homogene Verteilung des Materials auf der unregelmäßigen Oberfläche.
Wie können wir Ihnen helfen?
Wenn Sie eine kostenlose Beratung wünschen oder sich zur Auswahl feuerfester Auskleidungen erkundigen möchten, hinterlassen Sie uns Ihre Kontaktdaten und wir rufen Sie an!
Senden Sie eine AnfrageWie lässt sich das Abplatzen von Feuerfeststeinen bei schnellen thermischen Zyklen minimieren?
Welcher Reparaturbeton bietet die höchste Abriebfestigkeit gegen flüchtige Partikel?
Wie schützt man die Auskleidung vor Korrosion durch Alkalien und Salzangriff?
Untere Zyklonstufen
Die unteren Zyklone sind entscheidend für die Zementklinkerproduktion – sie sorgen für intensives Mischen, Umlagern und Verteilen der Rohstoffe. In dieser Zone steigen die Temperaturen auf bis zu 950 °C, was deutlich höher ist als in den oberen Zyklonen. Ein wichtiger Aspekt ist die partielle Vor-Kalzinierung des Kalksteins, die die Effizienz der nachfolgenden Prozessschritte verbessert. Feuerfesttechnisch bestehen die unteren Zyklone ebenfalls aus drei Hauptzonen: Gewölbe, Zylinder und Konus. Die Auskleidung ist deutlich stärkeren Beanspruchungen ausgesetzt als in den oberen Zyklonen – sowohl thermisch, mechanisch als auch chemisch (z. B. durch Alkalien). Unter Standardbedingungen kommen multischamotthaltige Steine mit Andalusit- und Siliziumkarbid-Zusätzen aus den Linien EXTRATON und ABRAL zum Einsatz – sie bieten hohe Beständigkeit gegen Abrieb und Alkalien. Bei Betonauskleidungen werden GELCAST, MULCAST und NxGel empfohlen – sie sind besonders widerstandsfähig gegenüber alternativen Brennstoffen und aggressiven chemischen Umgebungen.
Angebotsumfang: Futterdesign Lieferung von feuerfesten Produkten Dienstleistungen im Bereich Auskleidungsinstallation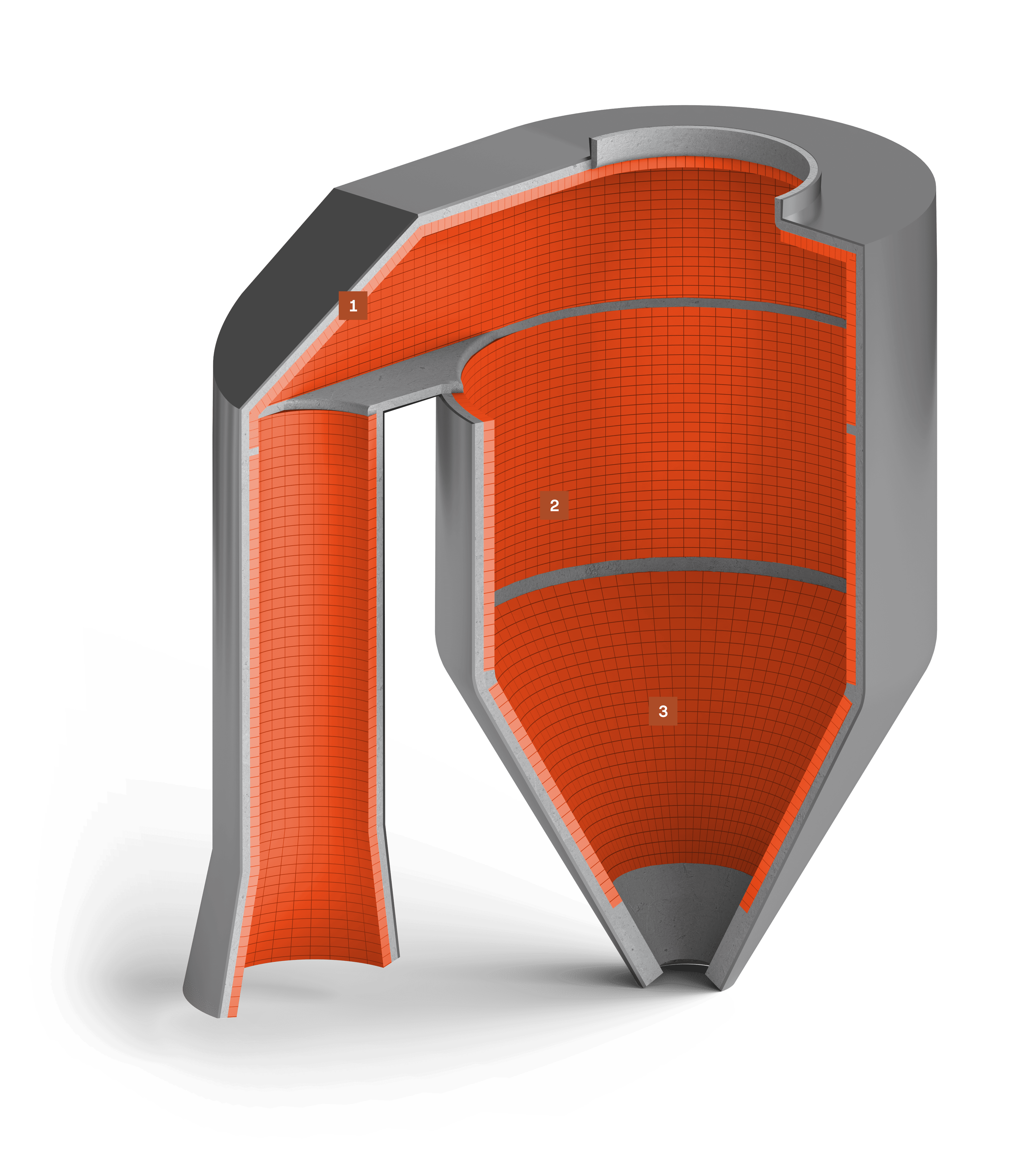
Das Gewölbe des unteren Zyklons ist v. a. gasgetragenem Abrieb durch flüchtige Partikel ausgesetzt. Obwohl Temperatur und mechanische Belastung relativ moderat sind, ist die Beanspruchung höher als im oberen Zyklon. Zusätzliche Herausforderungen: chemische Angriffe und Anbackungen, die die Auskleidung schädigen können. Die mehrschichtige Struktur mit Keilsteinen in Arbeits- und Dämmlagen gewährleistet gute Belastungsverteilung und Schutz.
Der Zylinderbereich ist einer Kombination aus Abrieb, mechanischen Belastungen und aggressiven chemischen Angriffen – v. a. durch Alkalien – ausgesetzt. Die Auskleidung muss sowohl mechanischer Erosion als auch chemischer Degradation widerstehen. Auch hier kommt eine mehrschichtige Struktur mit Keilsteinen zum Einsatz, die eine lange Standzeit ermöglicht.
Stożek, jako fragment cyklonu dolnego, jest najbardziej obciążoną strefą pod względem oddziaływań mechanicznych, chemicznych oraz ściernych. Ze względu na trudności wynikające z nietypowego kształtu stożka oraz utrudnioną technologię murowania, obmurze w tej strefie wykonuje się z betonu. Takie rozwiązanie pozwala na precyzyjne dopasowanie materiału do skomplikowanej geometrii stożka, co minimalizuje ryzyko powstawania nierównomiernych naprężeń i miejscowych uszkodzeń. W strefie stożka kluczowym aspektem jest zapewnienie odporności na zarówno mechaniczne, jak i chemiczne oraz ścierne obciążenia.
Wie können wir Ihnen helfen?
Wenn Sie eine kostenlose Beratung wünschen oder sich zur Auswahl feuerfester Auskleidungen erkundigen möchten, hinterlassen Sie uns Ihre Kontaktdaten und wir rufen Sie an!
Senden Sie eine AnfrageWelcher Feuerfestbeton bietet die beste Balance zwischen Abriebfestigkeit und Thermoschock-Toleranz?
Wie kann man die Differenz in der Ausdehnung zwischen Keramikauskleidung und Stahlmantel kompensieren, um Risse zu vermeiden?
Wie lassen sich Anbackungen von Staub auf der Auskleidung wirksam reduzieren?
Kalzinator
Der Kalzinator, hauptsächlich für das Vorwärmen und Kalzinieren von Kalksteinrohstoffen zuständig, verlagert einen Teil des Brenn- und Entkohlungsprozesses aus dem Drehrohrofen in die Wärmetauschertürme. Durch den Einsatz alternativer Brennstoffe trägt er zur Reduktion von Emissionen und Betriebskosten bei. Die Betriebsbedingungen sind jedoch deutlich anspruchsvoller und erfordern entsprechend leistungsfähige feuerfeste Materialien. Im Kalzinator herrschen Temperaturen zwischen 800 °C und 1100 °C. Die Kanäle sind sowohl hohen Temperaturen als auch korrosiven Medien ausgesetzt – darunter SOₓ, NOₓ, Alkalien, Chlor und Schwefel. Diese führen zu abrasivem Verschleiß der Auskleidung. Daher kommen niederzementhaltige oder zementfreie Feuerbetone mit Zusätzen wie Zirkonoxid (ZrO₂) und Siliziumkarbid (SiC) zum Einsatz; für Reparaturen auch Spritzbetone. Bei der Verwendung von Steinen empfehlen sich hochaluminahaltige Produkte mit Beständigkeit gegen chemischen Angriff, hohe Temperaturen und Thermoschocks. Die Kalzinatorauskleidung ist mehrschichtig aufgebaut: mit einer Arbeits-, Schutz- und Dämmungsschicht, um Langlebigkeit unter extremen Bedingungen zu gewährleisten. Die Standzeit variiert je nach Betriebsparametern und Anteil alternativer Brennstoffe von mehreren Jahren.
Angebotsumfang: Futterdesign Lieferung von feuerfesten Produkten Dienstleistungen im Bereich Auskleidungsinstallation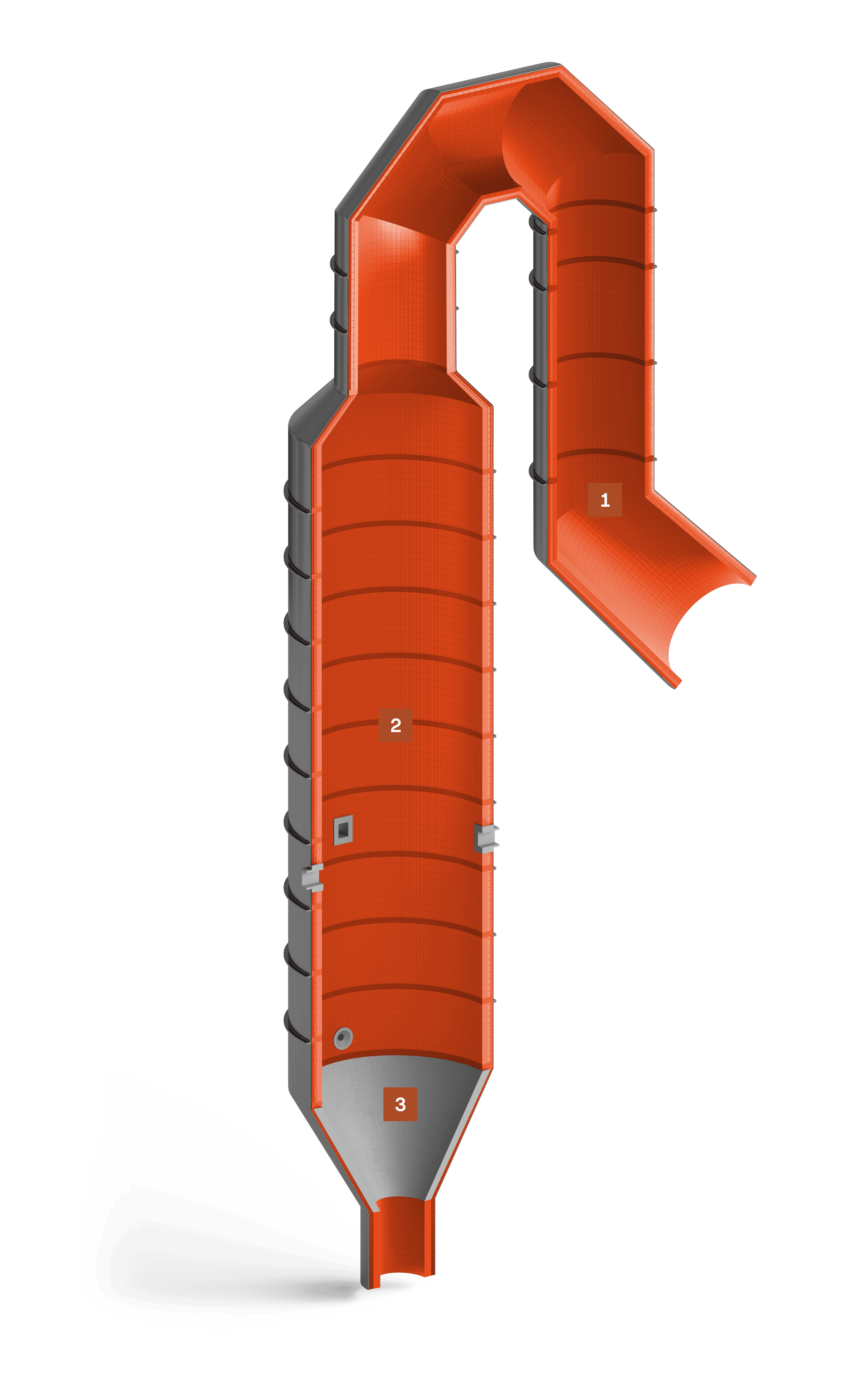
In dieser Zone herrschen Temperaturen zwischen etwa 700 und 900 °C. Die Hauptgefahren für die Auskleidung sind mechanische Abrasion und chemische Erosion – bedingt durch den Eintritt von Rohmehl. Häufig kommt es zu Anbackungen durch Schwefel und Chlor (bei alternativen Brennstoffen). Es empfiehlt sich der Einsatz hochaluminahaltiger Feuerbetone mit ZrO₂- oder SiC-Zusätzen. Bei gemauerter Auskleidung sind hochalumina Steine mit hoher Abrieb- und Thermoschockbeständigkeit die beste Wahl.
In dieser Zone überschreiten die Temperaturen 1000 °C, im Bereich der Brenner sogar bis zu 1200 °C. Dies ist eine der extremsten Zonen für Feuerfestmaterialien im gesamten Zementwerk. Der Prozess – meist mit 100 % alternativen Brennstoffen – verursacht starken Alkalieinfluss auf die Auskleidung. Verwendet werden hochaluminahaltige Steine und Betone mit Zusätzen wie Zirkonoxid oder Siliziumkarbid zur Erhöhung der Beständigkeit gegen chemischen Angriff und Abrieb.
Hier herrschen weiterhin Temperaturen um 1000 °C. Das Hauptrisiko geht jedoch von Alkalien aus, die in der darüberliegenden Brennzone entstehen. Eingesetzt werden niederzement- oder zementfreie hochaluminahaltige Feuerbetone. Bei gemauerter Auskleidung empfiehlt man hochaluminahaltige Steine mit SiC-Zusätzen. Die Auskleidung ist häufig chemisch verkrustet – diese Ablagerungen müssen regelmäßig mit Luft oder Wasser entfernt werden. Die Materialien müssen auch mechanischen Aufprallkräften standhalten, da sich Ablagerungen aus höheren Zonen lösen und auf die schräge Engstelle prallen.
Wie können wir Ihnen helfen?
Wenn Sie eine kostenlose Beratung wünschen oder sich zur Auswahl feuerfester Auskleidungen erkundigen möchten, hinterlassen Sie uns Ihre Kontaktdaten und wir rufen Sie an!
Senden Sie eine AnfrageWelche Spritzmasse ist abriebfest gegen gesinterten Klinker und beständig gegen CO₂-Korrosion?
Welches Material eignet sich am besten für häufige Start-Stopp-Zyklen und Thermoschocks?
Wie lässt sich die Brennerposition im Design berücksichtigen, um lokale Überhitzung am Stahlmantel zu vermeiden?
Tertiärluftkanal (TAD)
Im Tertiärluftkanal (TAD), wo die Temperaturen von etwa 1000 °C im heißen Bereich bis auf 600 °C im kühleren Bereich sinken, herrschen anspruchsvolle Betriebsbedingungen. Dieser Kanal führt einen zusätzlichen Luftstrom in den Prozess ein, was nicht nur die Verbrennungseffizienz verbessert, sondern auch eine präzise Regelung der Ofeninnentemperatur ermöglicht. Um eine optimale Prozessleistung zu erreichen, können zentrale Parameter wie Luftdurchsatz, Temperatur oder Druck mithilfe fortschrittlicher Überwachungs- und Steuerungssysteme dynamisch angepasst werden.
Angebotsumfang: Futterdesign Lieferung von feuerfesten Produkten Dienstleistungen im Bereich Auskleidungsinstallation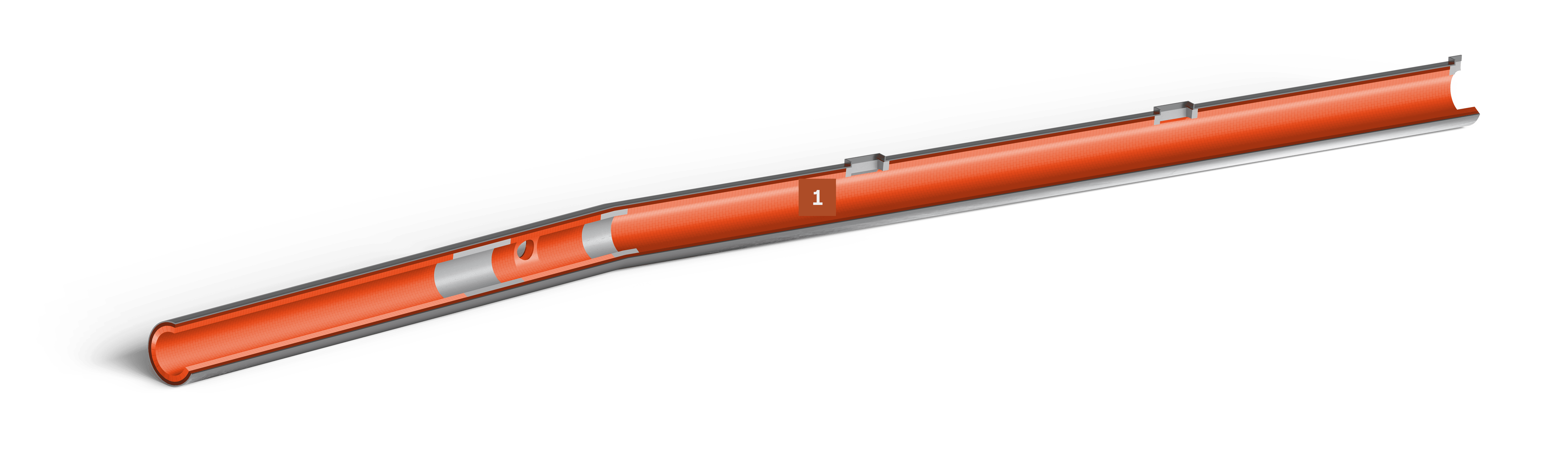
Die Herausforderung bei der Auskleidung des Tertiärluftkanals liegt im kleinen Durchmesser, der die Wirkung der abrasiven Umgebung verstärkt – Partikel strömen mit hoher Geschwindigkeit und unter Druck durch das Rohr. Zur Erhöhung der Standzeit empfiehlt PCO die Verwendung von geformten EXTRATON-Steinen sowie PCOCAST-Schamottbeton mit Zusätzen wie Siliziumkarbid oder Zirkon zur Abriebfestigkeit. Für noch anspruchsvollere Bedingungen wie höheren Druck oder höhere Temperaturen wird der Einsatz von ABRAL-Schamottsteinen mit Siliziumkarbid-Zusätzen empfohlen.
Wie können wir Ihnen helfen?
Wenn Sie eine kostenlose Beratung wünschen oder sich zur Auswahl feuerfester Auskleidungen erkundigen möchten, hinterlassen Sie uns Ihre Kontaktdaten und wir rufen Sie an!
Senden Sie eine AnfrageWie gestaltet man die Dämmung so, dass die Temperatur der Außenhülle z. B. unter 200 °C bleibt?
Welcher Feuerfestmörtel sorgt für stabile Fugenverbindungen der Arbeitslage bei hohem Luftdruck?
Welches Material eignet sich für die Auskleidung von Rohrbögen?
Rura wzniosu i komora wlotowa do pieca
Rura wzniosu i komora wlotowa to elementy instalacji cementowniczej odpowiadające za przenoszenie wstępnie podgrzanego materiału z cyklonów do pieca obrotowego, gdzie surowiec jest dalej podgrzewany. Zakres temperatur pracy to od około 500°C w górnej części rury wzniosu do 1100°C na przejściu do pieca obrotowego. Ponadto, komora wlotowa (nazywana też komorą dymową) odbiera gorące spaliny z pieca i przekazuje je do układu cyklonów, umożliwiając recyrkulację ciepła. Czynnikami ryzyka dla poprawnej pracy wymurówki są agresywne gazy (atak alkaliów), udary mechaniczne oraz ścieranie spowodowane przesuwaniem materiału, co staje się szczególnie problematyczne w instalacjach z kalcynatorem, gdzie udział paliw alternatywnych jest większy. Dlatego wyłożenie ogniotrwałe powinno charakteryzować się niską porowatością i wysoką odpornością na ścieranie. PCO Żarów oferuje kompletne rozwiązania od projektu do montażu, dostarczając cegły i betony ogniotrwałe o zawartości Al₂O₃ w zakresie od 30% do 60%, wzbogacone o dodatki zwiększające odporność na czynniki chemiczne i ścieranie.
Angebotsumfang: Futterdesign Lieferung von feuerfesten Produkten Dienstleistungen im Bereich Auskleidungsinstallation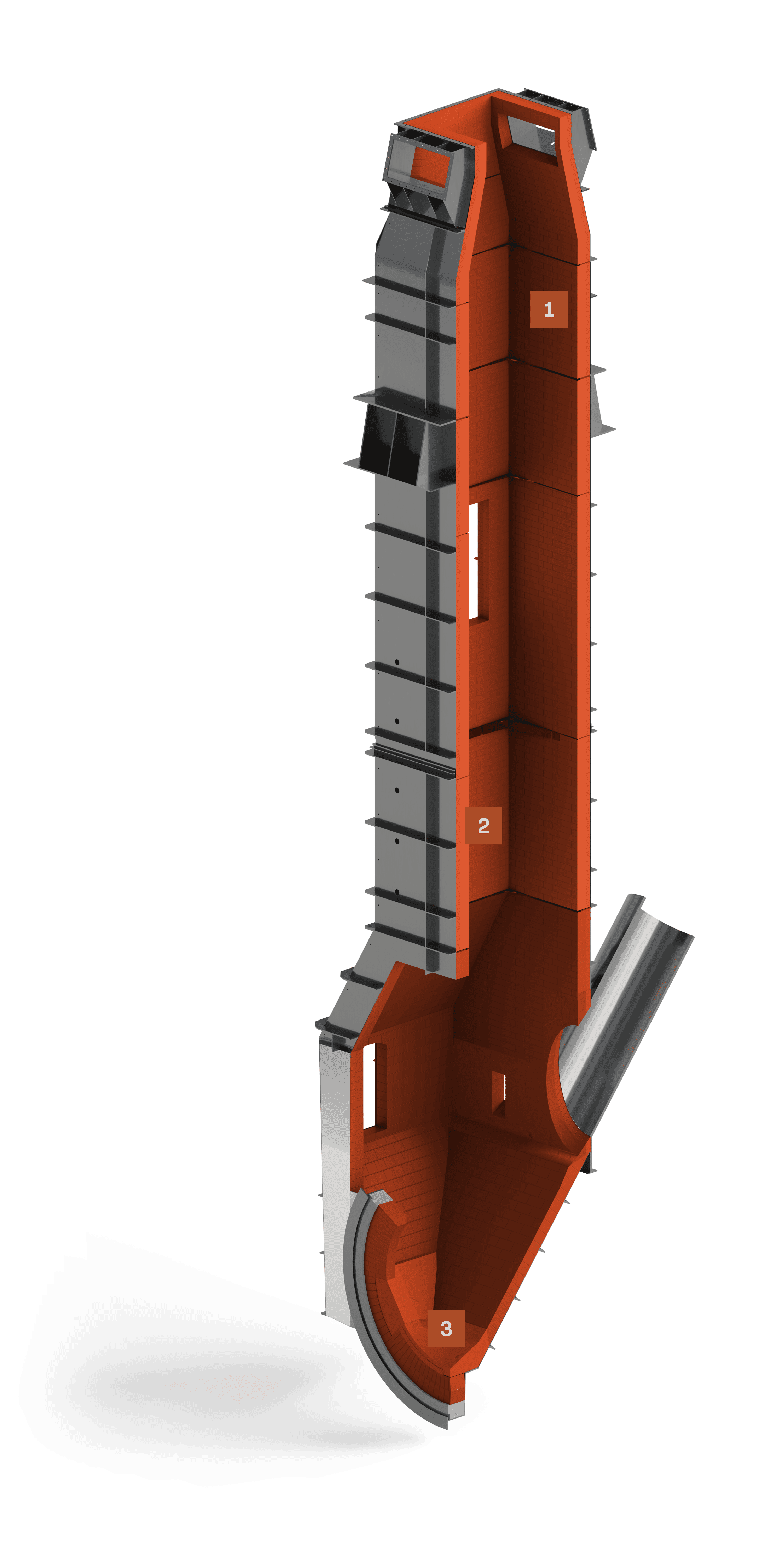
Im oberen Bereich des Steigrohrs (bis 700 °C) kommen als Arbeitslage Schamottsteine zum Einsatz. PCO empfiehlt EXTRATON oder ABRAL mit erhöhter Abriebfestigkeit. Bei anspruchsvolleren Bedingungen kann zusätzlich die bauxitbasierte Hochaluminasteinqualität BAUXITEX verwendet werden, um den Schutz zu erhöhen.
Hier steigen die Temperaturen auf bis zu 1100 °C und es treten intensive chemische Angriffe auf. Verwendet werden Hochaluminasteine auf Andalusit- oder Bauxitbasis, ergänzt durch Zusätze zur Erhöhung der mechanischen und chemischen Widerstandsfähigkeit. PCO empfiehlt ABRAL-, ANDALUX- oder ultraniederzementhaltige NxGel-Betone, die für schnelles Aufheizen geeignet sind.
Die Einlaufkammer ist starken chemischen Angriffen durch heiße Abgase ausgesetzt und gleichzeitig mechanischen Stößen – das fallende Material schlägt beim Übergang vom Steigrohr zur Kammer auf. Das führt zu starker Abrasion. Zudem sind Anbackungen durch Rohmehl typisch, die lokale Verstopfungen verursachen können. Die Auskleidung sollte Zusätze wie Siliziumkarbid oder Zirkon enthalten, um Schlagfestigkeit zu gewährleisten und Anhaftungen zu vermeiden – also niedrige Porosität und geringe Benetzbarkeit. So wird ein freier Materialfluss zum Drehrohrofen ermöglicht.
Wie können wir Ihnen helfen?
Wenn Sie eine kostenlose Beratung wünschen oder sich zur Auswahl feuerfester Auskleidungen erkundigen möchten, hinterlassen Sie uns Ihre Kontaktdaten und wir rufen Sie an!
Senden Sie eine AnfrageWelches Material verbessert die Beständigkeit gegen chemische Prozessrückstände?
Wie lässt sich die Erosion an der Übergangsstelle vom Kanal zur Kammer bei hohen Strömungsgeschwindigkeiten reduzieren?
Welches Material hält Thermoschocks stand, ohne dass Fugen aufreißen?
Hauptbrenner
In diesem Bereich – wo Temperaturen von über 1500 °C auftreten – ist die feuerfeste Auskleidung extremen Bedingungen ausgesetzt: rasche Temperaturwechsel, intensive Wärmestrahlung sowie der Angriff durch Oxidationsmittel und Schwefelverbindungen. Dies erfordert Materialien mit außergewöhnlicher Beständigkeit gegenüber chemischer Korrosion und Thermoschocks. Die keramische Auskleidung des Brenners schützt nicht nur die Stahlstruktur vor Degradation, sondern gewährleistet auch ein effektives Wärmemanagement – sie minimiert Wärmeverluste und steigert die Verbrennungseffizienz. In dieser Zone werden Auskleidungen vergleichsweise häufig erneuert – der Wartungszyklus reicht von wenigen Monaten bis maximal zu einem Jahr.
Angebotsumfang: Futterdesign Lieferung von feuerfesten Produkten Dienstleistungen im Bereich Auskleidungsinstallation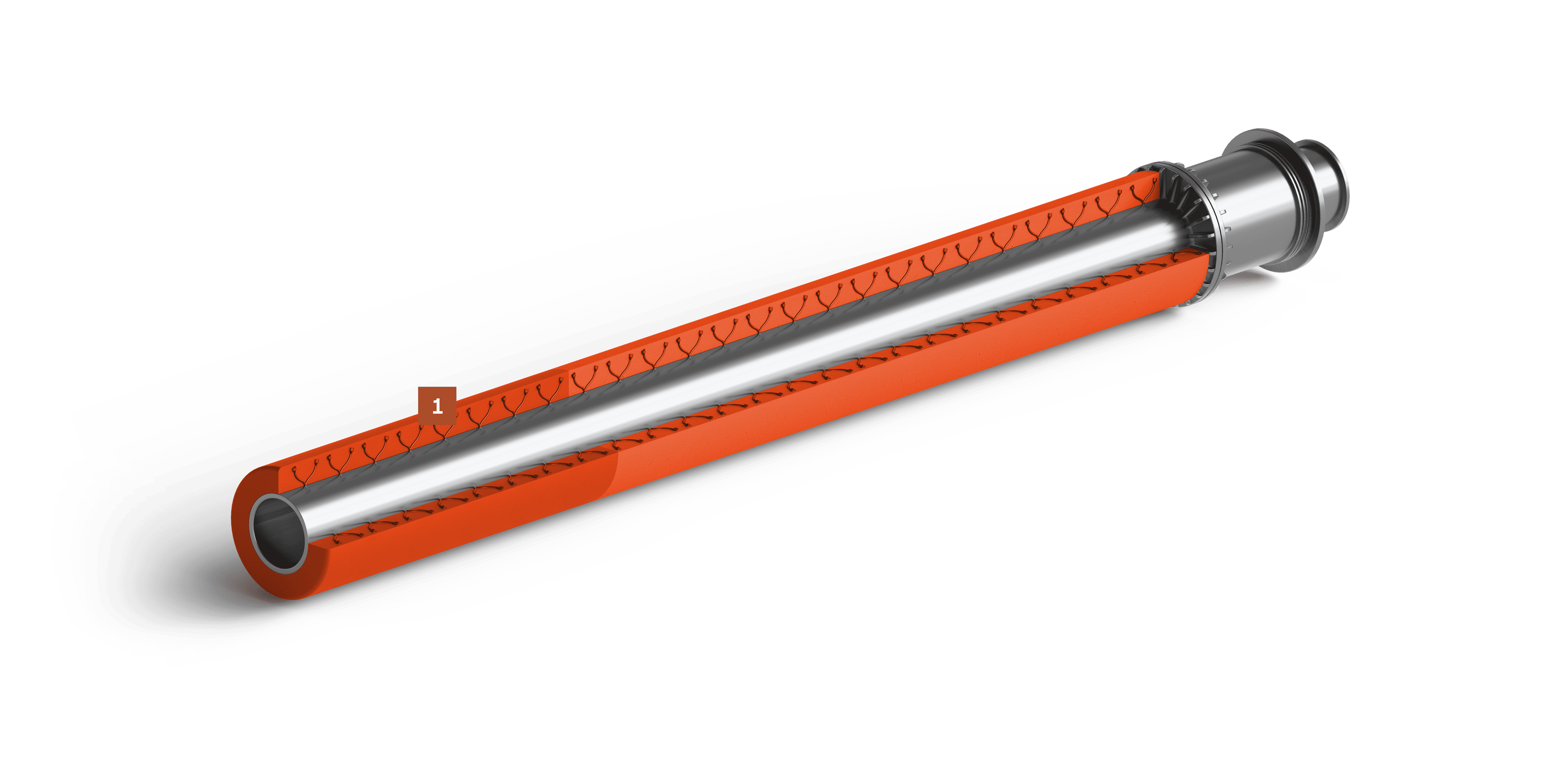
In der Flammenzone herrschen extrem hohe Temperaturen sowie ein aggressives Wirkungsumfeld durch alternative Brennstoffe – beides erfordert häufige Wartung. Die Anwendung des Betons in dieser Zone ist technisch anspruchsvoll, insbesondere beim direkten Gießen am Brenner. Sie verlangt spezielle Technologien sowie erfahrene Handwerker. Entscheidend ist eine homogene Betonmischung, die eine gleichmäßige Verteilung ermöglicht und ein schnelles Aufheizen sicherstellt – beides ist essenziell für einen kontinuierlichen Ofenbetrieb. Aufgrund der extremen Bedingungen muss das Material höchste Thermoschock- und Brennstoffresistenz aufweisen.
Wie können wir Ihnen helfen?
Wenn Sie eine kostenlose Beratung wünschen oder sich zur Auswahl feuerfester Auskleidungen erkundigen möchten, hinterlassen Sie uns Ihre Kontaktdaten und wir rufen Sie an!
Senden Sie eine AnfrageWie gestaltet man Brennerformsteine, um ein Durchbrennen zu vermeiden?
Welches keramische Material hält thermischen Spannungen am besten stand?
Wie plant man den Inspektionszyklus der Brennerauskleidung, um frühzeitig übermäßigen Verschleiß zu erkennen?
Drehrohrofen für Zementklinker
Die Hauptfunktion des Drehrohrofens in der Zementklinkerproduktion besteht darin, das Rohmaterial auf sehr hohe Temperaturen zwischen 1350 und 1450 °C zu erhitzen. Dieser Prozess führt zur Kalzinierung und zu den chemischen Reaktionen, durch die sich die klinkertypischen Minerale bilden. Die feuerfeste Auskleidung des Ofens ist zahlreichen Belastungen ausgesetzt. Dazu zählen abrasive Beanspruchung, thermische Spannungen durch die Hitzeeinwirkung von Material und Brenner sowie mechanische Belastungen infolge der Rotation des Stahlmantels. Hinzu kommt chemische Korrosion, die durch den Kontakt mit dem Rohmaterial, den Verbrennungsgasen und den bei der Nutzung alternativer Brennstoffe entstehenden Schlacken verursacht wird. Darüber hinaus greifen aggressive chemische Verbindungen die Auskleidung zusätzlich an. Für diese anspruchsvollen Bedingungen bietet PCO Żarów ein umfassendes Portfolio an Materialien und Dienstleistungen an. Dazu gehören hochaluminahaltige Produkte mit Siliziumkarbid-Zusätzen, die eine erhöhte Beständigkeit gegenüber chemischer Korrosion, Abrieb und Thermoschock aufweisen. Ebenso zählen chemisch gebundene Andalusitprodukte mit besonders hoher Lebensdauer sowie schamott- und hochaluminahaltige Steine mit verbesserter Abrieb- und Korrosionsbeständigkeit zum Angebot.
Angebotsumfang: Futterdesign Lieferung von feuerfesten Produkten Dienstleistungen im Bereich Auskleidungsinstallation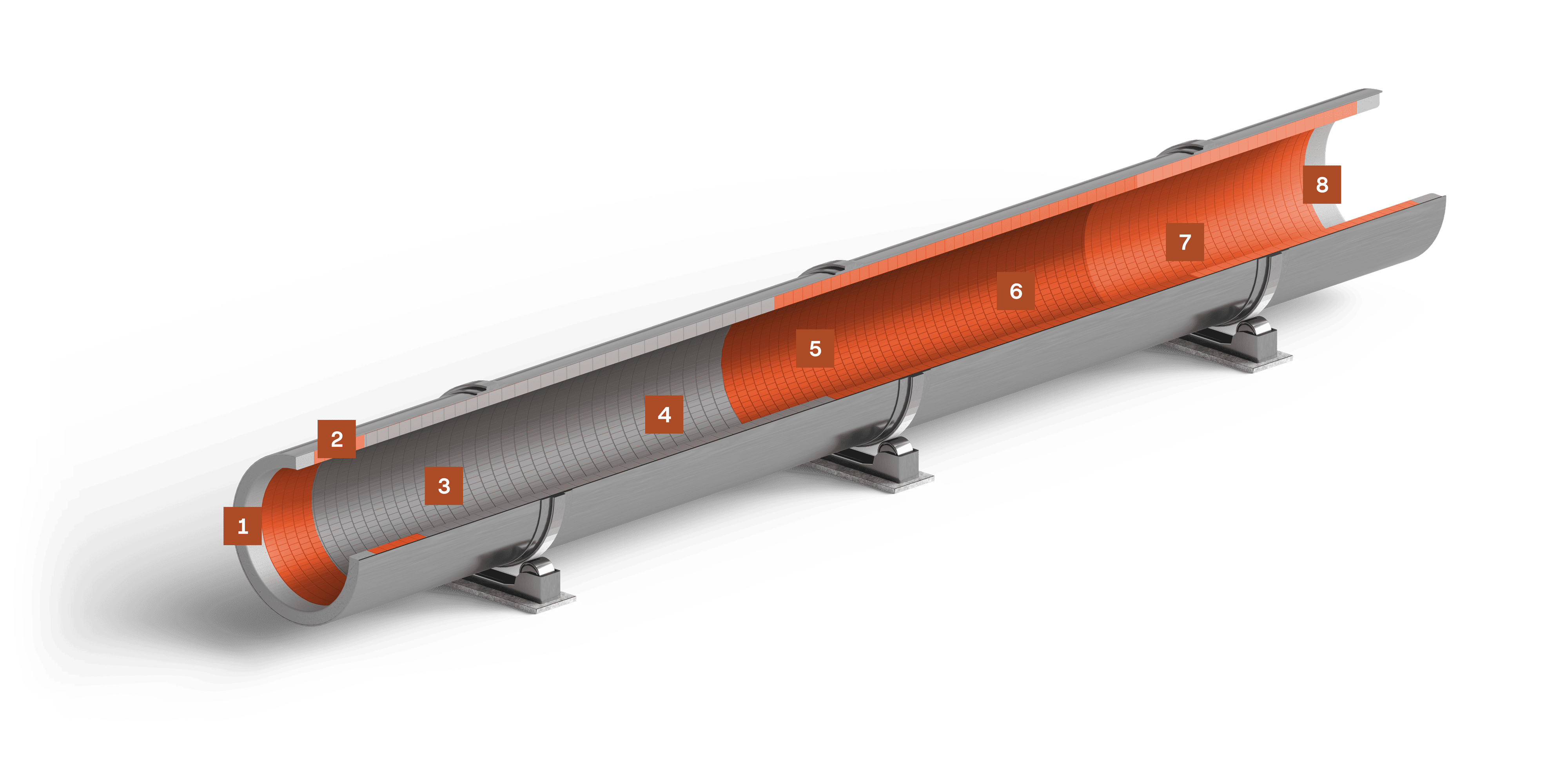
Diese Endzone des Ofens – auch als „Nose Ring“ bekannt – weist Bedingungen auf, die denen der Ofenaustrittszone ähneln. Die Temperaturen schwanken stark, und das verarbeitete Material übt einen hohen mechanischen Druck aus. Aufgrund der Konstruktion des Drehrohrofens werden in dieser Zone monolithische Produkte eingesetzt, die direkt vor Ort mit Beton gegossen werden. Entscheidend sind hier eine hohe Druck- und Abriebfestigkeit, um die strukturelle Integrität unter starker Belastung sicherzustellen. Empfohlen werden hochaluminahaltige Betone der Klasse MULCAST sowie niederzementhaltige Betone der Linie PCOCAST.
In der Kühlzone stellt die mechanische Belastung durch aufplatzenden Klinker die größte Herausforderung dar. Das Material verändert sein Volumen infolge plötzlicher Temperaturschwankungen, was zu Stößen gegen die Auskleidung führt. Die Temperaturen liegen in dieser Zone zwischen 900 und 1100 °C. Das Mauerwerk besteht aus einer einzelnen Lage Keilsteine. Die hier eingesetzten feuerfesten Materialien müssen eine hohe Beständigkeit gegen thermische Schocks sowie außergewöhnliche mechanische Festigkeit gegenüber Stößen und Abrieb aufweisen.
In der unteren Übergangszone beginnt der in der Brennzone gesinterte Klinker abzukühlen, wobei die Temperaturen auf etwa 1200 °C sinken. Trotz des Temperaturabfalls werden weiterhin feuerfeste Produkte mit hoher Widerstandsfähigkeit gegenüber thermischen Schwankungen verwendet. In dieser Phase dominieren magnesit-spinelhaltige Produkte, die für eine durchgängige Schutzwirkung sorgen und gleichzeitig thermische Spannungen begrenzen.
Die Brennzone ist der heißeste Bereich des Drehrohrofens mit Temperaturen von bis zu 1500 °C. In dieser Zone finden die vollständigen chemischen Umwandlungen statt, bei denen der Kalkstein in Klinkerminerale übergeht. Aufgrund der extremen thermischen und chemischen Belastungen empfiehlt sich der Einsatz von Magnesit-Produkten, die speziell für diese Bedingungen entwickelt wurden.
In der oberen Übergangszone wirken sehr hohe Temperaturen von über 1200 °C. Diese Zone ist durch instabile und stark schwankende Bedingungen gekennzeichnet. Die Auskleidung besteht aus einer einzigen Lage Keilsteine und muss in der Lage sein, plötzlichen Temperaturwechseln standzuhalten. In dieser Zone kommen überwiegend Magnesit-Spinell-Produkte zum Einsatz. An der Grenze zur Sicherheitszone werden hochwertige Alumosilikatprodukte eingebaut, die optimalen Schutz gegen thermische Schocks bieten.
In der Sicherheitszone herrschen Temperaturen von über 1000 °C, was den Zerfall von Kalkstein begünstigt. Die Bedingungen variieren stark und hängen insbesondere vom Anteil an RDF-Brennstoffen (Ersatzbrennstoffen) im Prozess ab. Die Auskleidung – ausgeführt als einzelne Lage Keilsteine – ist Angriffen durch Alkalien, flüssige Eutektika, instabile Spannungen sowie chemische und thermische Belastungen durch Einsatzstoffe und Brenngase ausgesetzt. Die Materialwahl muss flexibel sein, um den wechselnden Bedingungen gerecht zu werden. Hier eignen sich hochaluminahaltige Produkte mit SiC-Zusätzen – z. B. ABRAL, ANDALUX oder chemisch gebundene BAUXITEX.
In der Kalzinierzone des Drehrohrofens treten neben intensiver mechanischer Abrasion durch die Bewegung des Materials auch chemische Belastungen durch Alkaliverbindungen aus Rohmaterialien und Brennstoffen auf. Die Temperaturen liegen zwischen 1000 und 1100 °C. Das Mauerwerk besteht aus einer einzigen Keillage. Die Materialien in dieser Zone müssen sowohl mechanisch hochfest als auch korrosionsbeständig sein, um einen störungsfreien Betrieb zu gewährleisten. Je nach Prozessbedingungen sind hier besonders Produkte der ABRAL-Serie geeignet, die eine erhöhte Beständigkeit gegenüber chemischem Angriff und mechanischem Verschleiß bieten.
Diese Zone markiert den Anfang der Ofenauskleidung. Hier stellt intensive mechanische Abrasion – verursacht durch die Bewegung des einströmenden Materials – das größte Risiko dar. Eingesetzt werden abriebfeste Betone. Entscheidend ist der Einsatz von hochaluminahaltigem Beton; empfohlen werden mittelzementhaltige MULCAST-Betone oder zementfreie GELCAST-Betone, die ausreichende Festigkeit und Widerstand gegen mechanische Beanspruchung bieten.
Wie können wir Ihnen helfen?
Wenn Sie eine kostenlose Beratung wünschen oder sich zur Auswahl feuerfester Auskleidungen erkundigen möchten, hinterlassen Sie uns Ihre Kontaktdaten und wir rufen Sie an!
Senden Sie eine AnfrageWie kann man die Formatwahl und das Verlegemuster der Steine optimieren, um Ringbildung und Klinkeranbackungen zu minimieren?
Welches Material eignet sich für den Einsatz in einem Ofen mit hohem Anteil an RDF-Brennstoffen?
Wie berücksichtigt man bei der Auskleidungsplanung die unregelmäßige Geometrie des Ofenmantels?
Kühler und Ofenkopf
Der Kühler und der Ofenkopf haben die Aufgabe, den Klinker nach dem Austritt aus dem Drehrohrofen abzukühlen. Im Ofenkopf können die Temperaturen bis zu 1100 °C erreichen, während sie im Kühler stufenweise von etwa 800 °C im heißen Bereich bis auf rund 100 °C im kalten Bereich sinken. Die Kühlerkonstruktion umfasst den Heißbereich, den Kaltbereich, das Dach (Gewölbe) und den sogenannten Bullnose-Ring. In allen Bereichen des Kühlers kommen alumosilikathaltige Feuerfestprodukte zum Einsatz. Der Ofenkopf ist insbesondere starken thermischen Schocks (durch aufplatzenden Klinker) sowie mechanischer Abrasion durch das Material in Bewegung ausgesetzt. Hinzu kommen thermische Wechsellasten sowie chemisch-aggressive und abrasive Prozessgase. Besonders verschleißanfällig ist der Bullnose-Ring, der sich im direkten Einflussbereich von heißen Gasen und Klinker befindet. PCO bietet ein breites Portfolio an Feuerfestmaterialien für Kühlerauskleidungen an, darunter Feuerbetone, vorgefertigte Betonelemente sowie bauxitbasierte Steine.
Angebotsumfang: Futterdesign Lieferung von feuerfesten Produkten Dienstleistungen im Bereich Auskleidungsinstallation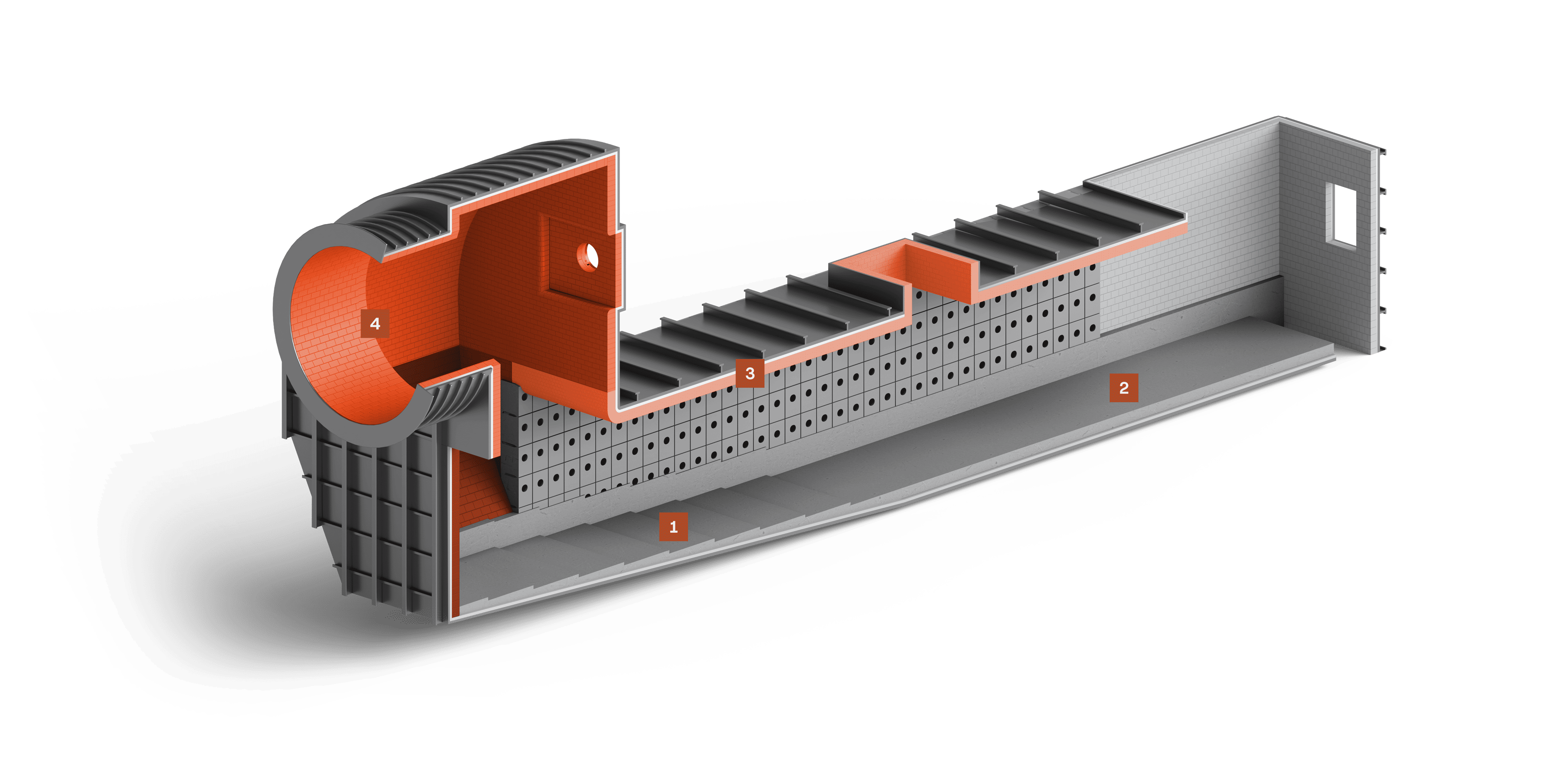
Im Heißbereich des Kühlers steigen die Temperaturen auf bis zu 1000 °C, bevor sie in Richtung des Rostes abrupt abfallen. Solche Bedingungen führen zu starken thermischen Schocks. Die Hauptbelastung für das Mauerwerk entsteht durch intensive mechanische Abrasion – verursacht sowohl durch die Bewegung des Klinkers als auch durch dynamische Luft- und Staubströme. Die Auskleidung wird hier mit vorgefertigten Betonelementen – sogenannten Stützwänden – ausgeführt. Diese bieten nicht nur thermische Isolierung, sondern auch mechanische Stabilität unter wechselnden Temperaturbedingungen. Entscheidend für eine zuverlässige Performance ist der Einsatz hochaluminahaltiger Betone mit hoher Thermoschock- und Abriebfestigkeit, die selbst bei starken Temperatursprüngen ihre Eigenschaften behalten.
Im Kaltbereich herrschen sehr stabile thermische Bedingungen – die Temperatur liegt unterhalb von 500 °C. Aufgrund der moderaten Belastung und geringen Wechselbeanspruchung ist der mechanisch-thermische Stress hier niedrig, weshalb die Auskleidung relativ selten erneuert werden muss. In dieser Zone wird Spritzbeton eingesetzt, der eine gleichmäßige, durchgehende Auskleidungsfläche bietet. Zusätzlich werden entlang des Rostes vorgefertigte Stützwände eingebaut, gefertigt aus feuerfesten Materialien niedrigerer Qualität wie MULCAST BN45M S5.
Das Gewölbe erstreckt sich sowohl über die heiße als auch die kalte Zone und ist Abrieb durch flüchtige Staubpartikel sowie thermischen Wechselbeanspruchungen über die gesamte Kühlerlänge ausgesetzt. Die eingesetzten Materialien müssen sowohl mechanisch als auch thermisch beständig sein. Im Heißbereich verbessern Zusätze wie SiC die Festigkeit der Auskleidung. Im kälteren Bereich liegt der Fokus auf struktureller Stabilität bei niedrigeren Temperaturen, um einen langfristigen Betrieb ohne häufige Wartung zu ermöglichen.
Der Ofenkopf dient der Übergabe des Klinkers in den Kühler – unter intensiver mechanischer und thermischer Beanspruchung. Besonderes Augenmerk liegt auf dem Bullnose-Ring, einer vertikalen Wand, die am stärksten belastet ist. Hier wirken mechanische Schläge durch herabfallenden Klinker in Kombination mit thermischen Wechsellasten. Im Ofenkopf kommen geformte Steine zum Einsatz, die thermische Stabilität und gute Isolierung bieten. Im Bereich des Bullnose-Rings hingegen werden – aufgrund der extremen mechanischen Belastung – hochwertige Feuerbetone oder vorgefertigte Betonelemente verwendet.
Wie können wir Ihnen helfen?
Wenn Sie eine kostenlose Beratung wünschen oder sich zur Auswahl feuerfester Auskleidungen erkundigen möchten, hinterlassen Sie uns Ihre Kontaktdaten und wir rufen Sie an!
Senden Sie eine AnfrageWelcher Feuerbeton bietet höchste Abriebfestigkeit im Bereich des Bullnose-Rings?
Wie schützt man die Auskleidung vor Schäden durch Thermoschocks bei Schwankungen des Kühlergasstroms?
Wie konstruiert man vorgefertigte Stützwände so, dass sie Vibrationen vom Rost effektiv standhalten?
Schachtöfen
Der Schachtofen, eingesetzt in der Kalkproduktion, arbeitet bei Temperaturen von häufig über 1100 °C. Der Kalzinierungsprozess erfordert eine gleichmäßige und kontrollierte Wärmeverteilung über die gesamte Ofenhöhe. Dem Ofen wird eine Mischung aus Kalkstein und Koks oder Anthrazit zugeführt. Die Verbrennung erzeugt die hohen Temperaturen, die notwendig sind, um Kalkstein in gebrannten Kalk (CaO) umzuwandeln. In der Sodaindustrie erfolgt die Kalkproduktion in Schachtöfen bei etwas niedrigeren Temperaturen als in der klassischen Kalkherstellung. Dadurch sinken auch die Anforderungen an feuerfeste Materialien und Heizungstechnik. In Zuckerfabriken dagegen herrschen besondere Betriebsbedingungen – häufige Temperaturwechsel und Stillstände führen zu einem beschleunigten Verschleiß der Auskleidung. Daher müssen hier besonders widerstandsfähige Feuerfestmaterialien eingesetzt werden, die zyklischen Temperaturschwankungen standhalten, ohne sich übermäßig abzunutzen. In solchen Anlagen erfolgt die Kalzinierung nicht kontinuierlich, was sie grundlegend von Schachtöfen in der klassischen Kalk- oder Sodaindustrie unterscheidet.
Angebotsumfang: Futterdesign Lieferung von feuerfesten Produkten Dienstleistungen im Bereich Auskleidungsinstallation
Die Vorwärmzone ist der Bereich, in dem zyklisch Kalkstein gemischt mit Brennstoff eingefüllt wird. Diese Bewegung verursacht intensive Abrasion, begleitet von hohen Temperaturen. Die verwendeten Materialien müssen daher besonders abriebfest sein – hier bewähren sich alumosilikatische EXTRATON-Produkte. Zur Minimierung von Wärmeverlusten wird eine Dämmschicht aus ISOLUX-Produkten in Kombination mit Mineralwolle eingesetzt, die hervorragende thermische Isolationseigenschaften bietet. Entscheidend ist die Kombination aus mechanischer Festigkeit und Dämmleistung, um die Lebensdauer der Auskleidung zu verlängern und gleichzeitig optimale Wärmeverhältnisse im Ofen aufrechtzuerhalten.
Die Brennzone – oft gleichgesetzt mit der Kalzinierzone – ist der Bereich intensiver thermischer Behandlung, in dem Kalkstein oder Dolomit unter hohem Temperatureinfluss umgewandelt wird. Die genaue Temperatur und die Zusammensetzung des Einsatzmaterials bestimmen die Art der chemischen und thermischen Belastung – einschließlich des Risikos von Hydratation. Normalerweise sind Aluminium- (Al₂O₃) und Siliziumoxide (SiO₂) chemisch stabil, doch die Auskleidung muss auch bei Feuchtigkeit formstabil bleiben. In dieser Zone sind Materialien mit hoher Hydratationsbeständigkeit und chemischer Stabilität bei hohen Temperaturen erforderlich. Besonders geeignet sind Produkte wie MULITEX, ANDALUX und BAUXITEX, die unter wechselnden Bedingungen zuverlässigen Schutz bieten.
In der Kühlzone sinkt die Temperatur stufenweise. Die thermische Belastung ist zwar geringer, dennoch ist eine gute Abriebfestigkeit erforderlich. In Einwellenöfen erfolgt die Abkühlung gleichmäßig über die gesamte Höhe, was den Einsatz homogener Dämmlösungen erlaubt. Am besten geeignet sind Schamottsteine, die hohe Druck- und Abriebfestigkeit aufweisen. Empfohlen werden SUPERTON-Produkte, speziell entwickelt für diesen Bereich. Die Dämmung besteht in Einwellenöfen aus ISOLUX-Modulen, ergänzt durch Mineralwolle, die eine durchgängige thermische Barriere bilden und Wärmeverluste reduzieren.
Wie können wir Ihnen helfen?
Wenn Sie eine kostenlose Beratung wünschen oder sich zur Auswahl feuerfester Auskleidungen erkundigen möchten, hinterlassen Sie uns Ihre Kontaktdaten und wir rufen Sie an!
Senden Sie eine AnfrageWelche hochaluminahaltigen Steine sind am beständigsten gegen chemische Zersetzung durch längere CO₂-Exposition im Schachtofen?
Welche Spritz- oder Stampfmassen bieten optimalen Widerstand gegen wiederholte Hydratation und Dampfangriff durch feuchtes Kalkmaterial?
Wie optimiert man Steinformate, Ankerkonstruktion und Fugenführung bei hohen Schachtgeometrien, um axiale Ausdehnung auszugleichen und Einstürze der Auskleidung zu vermeiden?
Maerz-Ofen – Lösungskonzept
Der Maerz-Ofen wird in Prozessen eingesetzt, bei denen eine präzise Temperaturkontrolle und eine gleichmäßige Wärmeverteilung erforderlich sind. Die feuerfeste Auskleidung ist dabei extrem hohen Temperaturen ausgesetzt – oft über 1200 °C. Ein wesentliches Merkmal, das den Maerz-Ofen von klassischen Schachtöfen unterscheidet, ist das sogenannte Reversierprinzip. Dabei sind zwei Schächte im Einsatz: einer für die Kalzinierung des Kalksteins, der andere zur Zufuhr der Verbrennungsluft. Die Umkehrung des Prozesses – erst Verbrennung, dann Kalzinierung, und im nächsten Zyklus umgekehrt – ermöglicht eine präzisere Temperaturregelung und bessere Energieausnutzung durch den alternierenden Gasstrom. Aufgrund der höheren Effizienz und der härteren Betriebsbedingungen ist der Einsatz hochwertigerer Feuerfestmaterialien als in herkömmlichen Schachtöfen erforderlich. Diese Materialien müssen hohe Thermoschock- und chemische Beständigkeit aufweisen, um die Integrität des Mauerwerks bei wechselnden Belastungen sicherzustellen. Die Optimierung der Wärmedistribution und die Minimierung von Energieverlusten sind entscheidend für die Effizienz der Technologie und die Langlebigkeit der Anlage.
Angebotsumfang: Futterdesign Lieferung von feuerfesten Produkten Dienstleistungen im Bereich Auskleidungsinstallation
Die Vorwärmzone im Maerz-Ofen reicht vom unteren Brennerniveau bis in den oberen Teil des Schachts, in den zyklisch Kalkstein-Feststoffgemisch eingefüllt wird. In dieser Zone wirken intensive abrasive und thermische Belastungen durch den direkten Kontakt des Einsatzmaterials mit der Auskleidung und durch wechselnde Temperaturverhältnisse. Deshalb ist in diesem Bereich besonders auf hohe Abriebfestigkeit und die Minimierung von Wärmeverlusten zu achten. Die Auskleidung wird je nach Temperaturprofil mit unterschiedlichen Materialien ausgeführt: Im unteren Bereich (bei den Brennern) kommen Magnesit-Spinell-Produkte zum Einsatz, die gegen Abrieb und aggressive Verbrennungsprodukte resistent sind. Im oberen Bereich werden EXTRATON-Alumosilikatsteine mit hoher Abriebfestigkeit verwendet.
Für einen kontrollierten Übergang zwischen der Magnesit-Spinell-Auskleidung und der Alumosilikatschicht wird eine Zwischenlage aus hochtonerdehaltigen Andalusit-Produkten eingebracht. Der Raum zwischen Stahlmantel und Arbeitslage wird mit einem mehrlagigen Dämmkonzept ausgekleidet, das aus ISOLUX-Dämmplatten und Mineralwollmatten besteht. In einigen Ausführungen wird zusätzlich eine Dämmzwischenlage aus SUPERTON oder EXTRATON zwischen Arbeits- und Hauptdämmung eingebaut. Die gesamte Auskleidung wird mit einer konventionellen Betonschicht abgeschlossen, die als mechanische Schutzschicht dient.
Die Brennzone erstreckt sich vom unteren Bereich der Tragegewölbe bis zum unteren Rand der Brennerlanzen. In diesem Abschnitt wird der Einsatzstoff intensiv gebrannt – bei sehr hohen Temperaturen und abhängig vom verwendeten Material (Kalkstein, Dolomit) auch unter aggressiven chemischen Einflüssen. PCO Żarów liefert hier Schutz- und Dämmmaterialien, die mit speziellen Formsteinen (Typen AS1, AS2 u. ä.) aus MULITEX oder ANDALUX ausgeführt werden. Diese Lösung sichert strukturelle Stabilität und Betriebssicherheit bei wechselnden Belastungsbedingungen.
Die Pfeilerstruktur sowie die darüberliegenden Tragegewölbe und Flachdecken werden aus niederzementhaltigen oder zementfreien Betonen gefertigt. Die Pfeiler selbst bestehen aus Formstein-Kombinationen wie VK-76x und WL-76, die hohe Tragfähigkeit gewährleisten. In pfeilerlosen Maerz-Öfen wird der Boden des hängenden Zylinders ebenfalls aus hochfesten Betonen hergestellt. Das Flachgewölbe erhält eine Dämmschicht aus leichten Isolierbetonen (z. B. ISOCAST, ISOGUN) ergänzt durch Mineralwolle.
Die Kühlzone reicht vom Beginn der Auskleidung bis zur Unterkante der Tragegewölbe. In diesem Bereich sinkt die Temperatur stufenweise ab, was für die thermische Stabilisierung entscheidend ist. Trotz sinkender Temperaturen bleibt die Auskleidung mechanisch und abrasiv stark beansprucht. Die Arbeitslage wird mit Schamottsteinen der Typen SUPERTON oder EXTRATON ausgeführt, die sich unter diesen Bedingungen bewähren. Der Zwischenraum zwischen den Pfeilern wird meist mit EXTRATON-Steinen gemauert. Die Dämmung basiert auf ISOLUX-Modulen, kombiniert mit Calciumsilikatplatten und Mineralwollmatten, um eine durchgängige thermische Barriere zu bilden.
Wie können wir Ihnen helfen?
Wenn Sie eine kostenlose Beratung wünschen oder sich zur Auswahl feuerfester Auskleidungen erkundigen möchten, hinterlassen Sie uns Ihre Kontaktdaten und wir rufen Sie an!
Senden Sie eine AnfrageWelche Pfeilerstein-Geometrie erhöht die mechanische Belastbarkeit der Auskleidung?
Welche Feuerfestmaterialien widerstehen gleichzeitig abrasivem und chemischem Angriff bei der Kalzinierung von Kalkstein?
Wie gestaltet man Übergangs- und Schutzlagen zwischen basischen und alumosilikatischen Materialien, um thermische Ausdehnung zu berücksichtigen und Auskleidungsschäden zu vermeiden?
Drehrohrofen für Kalk und Zellstoff
Der Kalkdrehrohrofen dient im Kraft-Verfahren der Rückgewinnung von Kalk aus Kalkschlämme, der anschließend in der Zellstoffproduktion eingesetzt wird. Die feuerfeste Auskleidung ist typischerweise zweischichtig aufgebaut und muss gleichzeitig hohe mechanische und thermische Belastungen aushalten. Die größten Herausforderungen für die Auskleidung sind schnelle Temperaturwechsel, chemische Reaktionen zwischen Kalkschlamm und Feuerfestmaterialien sowie Druck- und Spannungsschwankungen, die durch die Drehbewegung des Ofens entstehen. Je nach Ofenzone werden unterschiedliche Materialien verwendet: Im Ein- und Auslassbereich kommen Feuerbetone mit hoher Thermoschock- und Chemikalienbeständigkeit zum Einsatz, zusammen mit Schamott- und Andalusitsteinen. In der Brennzone werden chemisch gebundene Andalusitsteine mit P₂O₅-Zusatz verwendet, die gegen extreme Temperaturen, aggressive chemische Einflüsse und mechanische Belastung beständig sind.
Angebotsumfang: Futterdesign Lieferung von feuerfesten Produkten Dienstleistungen im Bereich Auskleidungsinstallation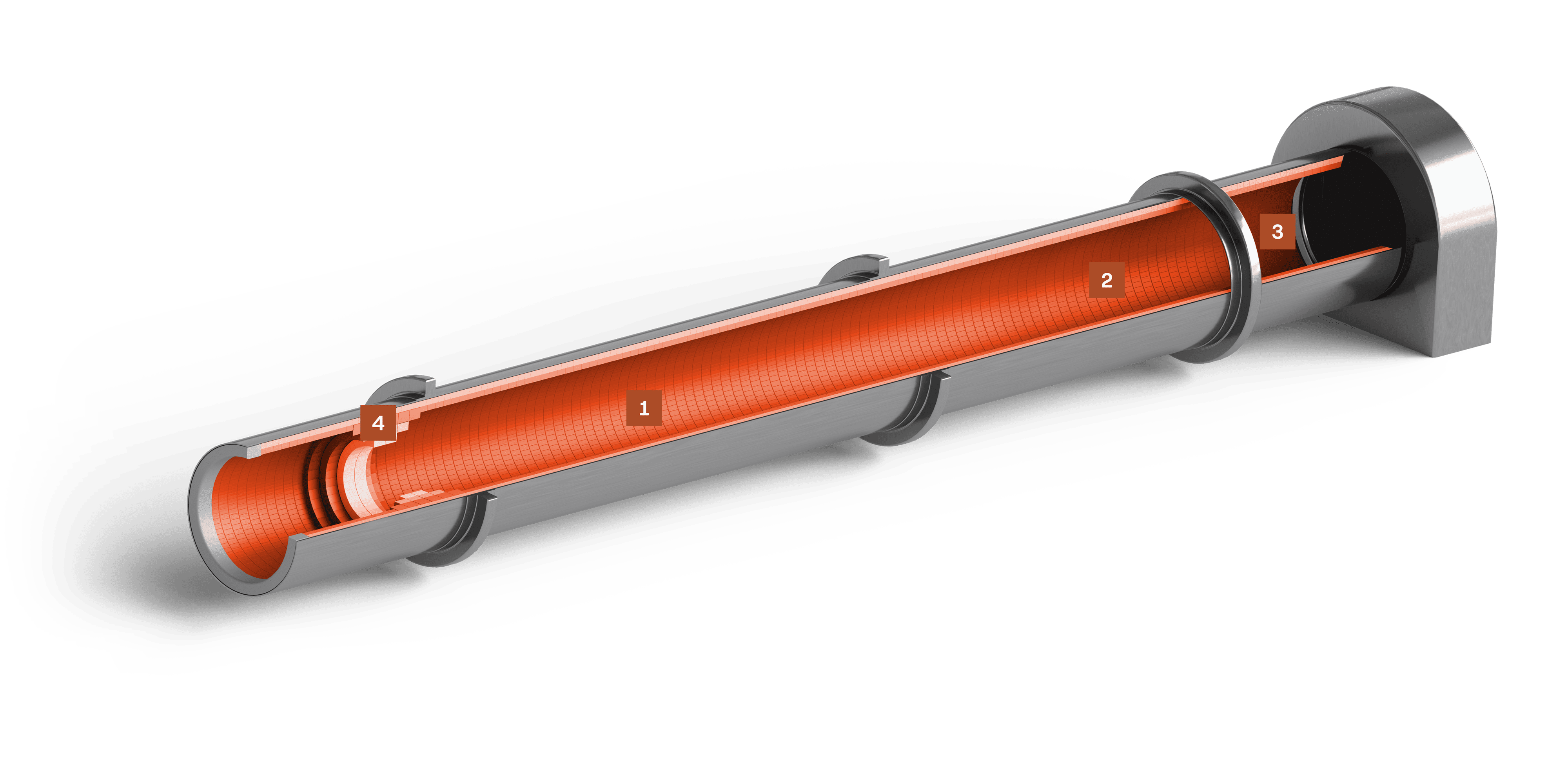
Die Vorwärmzone im Kalkdrehrohrofen umfasst den Temperaturanstieg von etwa 200 °C bis auf 1100 °C. In diesem Abschnitt wird die Kalkschlämme getrocknet und vorgekalziniert. Die feuerfeste Auskleidung ist hier Abrieb und chemischer Erosion ausgesetzt. Die Schlämme enthält alkalische Salze, Schwefelverbindungen und Chloride – diese können chemisch in die Auskleidung eindringen. Hinzu kommt die Feuchtigkeit des Einsatzmaterials (bis zu 20 %), weshalb das Mauerwerk gegen Wasseraufnahme beständig sein muss. Für die Arbeitslage empfiehlt sich der Einsatz von hochwertigen, niedrig porösen Schamottsteinen mit Alkalibeständigkeit – z. B. der Serie EXTRATON. Näher zur Brennzone, wo höhere Temperaturen auftreten, sind hochtonerdehaltige oder chemisch gebundene Produkte wie ANDALUX zu bevorzugen.
In dieser Zone herrschen Temperaturen zwischen 1100 °C und 1300 °C über die gesamte Länge. Die Betriebsbedingungen sind variabel – thermische Spannungen durch die Brennerflamme und chemische Angriffe durch die Prozessgase stellen die Hauptbelastungen dar. Die Kalkschlämme wird gesintert, wobei sie sich von einem karbonathaltigen Schlamm in reines gebranntes CaO umwandelt. Die Auskleidung muss Thermoschocks, hohe Temperaturen sowie chemisch und mechanisch aggressive Bedingungen aushalten. Hier wird eine zweischichtige Ausführung empfohlen. Für die Arbeitslage eignen sich chemisch gebundene Andalusitsteine der Klasse ANDALUX.
Dies ist der kürzeste Abschnitt des Drehrohrofens und liegt wenige Meter vor dem Übergang zum Kühler. Hier fällt die Temperatur schnell von 1000 °C auf etwa 200 °C ab – was zu extremen Thermoschocks führt. Das vollständig umgewandelte Kalkmaterial wirkt abrasiv auf das Mauerwerk. Durch die rotierende Bewegung und die konisch zulaufende Geometrie entstehen mechanische Spannungen, die für die Auskleidung gefährlich sein können. Die Auskleidung ist zweischichtig aufgebaut. In den verengten Bereichen kommt in der Arbeitslage ein hochtonerdehaltiger Feuerbeton, in der Dämmlage geformte ISOLUX-Dämmplatten mit erhöhter Druckfestigkeit zum Einsatz.
Die Stauschwelle besteht aus feuerfester Keramik und sorgt für eine gleichmäßige Verteilung des Materials am Auslass des Drehrohrofens. In dieser Zone wirken erheblicher Abrieb und mechanischer Druck auf die Auskleidung. Empfohlen wird der Einsatz von hochbelastbaren Andalusitsteinen, die den Materialfluss gezielt regulieren.
Wie können wir Ihnen helfen?
Wenn Sie eine kostenlose Beratung wünschen oder sich zur Auswahl feuerfester Auskleidungen erkundigen möchten, hinterlassen Sie uns Ihre Kontaktdaten und wir rufen Sie an!
Senden Sie eine AnfrageWelches Material eignet sich als Arbeitsauskleidung im Kontakt mit Teer und organischen Säuren?
Wie lässt sich die Auskleidung vor Rissbildung durch unterschiedliche Wärmeausdehnung von Stahlmantel, Dämmschicht und Arbeitslage schützen?
Wie lässt sich die Auskleidung vor Rissbildung durch unterschiedliche Wärmeausdehnung von Stahlmantel, Dämmschicht und Arbeitslage schützen?
Warum PCO wählen?
Feuerfestmontage im Paket mit Materiallieferung – einfacheres Projektmanagement und ein einziger Qualitätsgarant.
Vollständiges Sortiment an hochaluminahaltigen Produkten für die Zement- und Kalkindustrie
Wir verfügen über ein eigenes Team von Konstrukteuren und Projektanten, das bereit ist, jede Herausforderung zu meistern
Ausgewählte Produkte und Dienstleistungen für die Kokereiindustrie
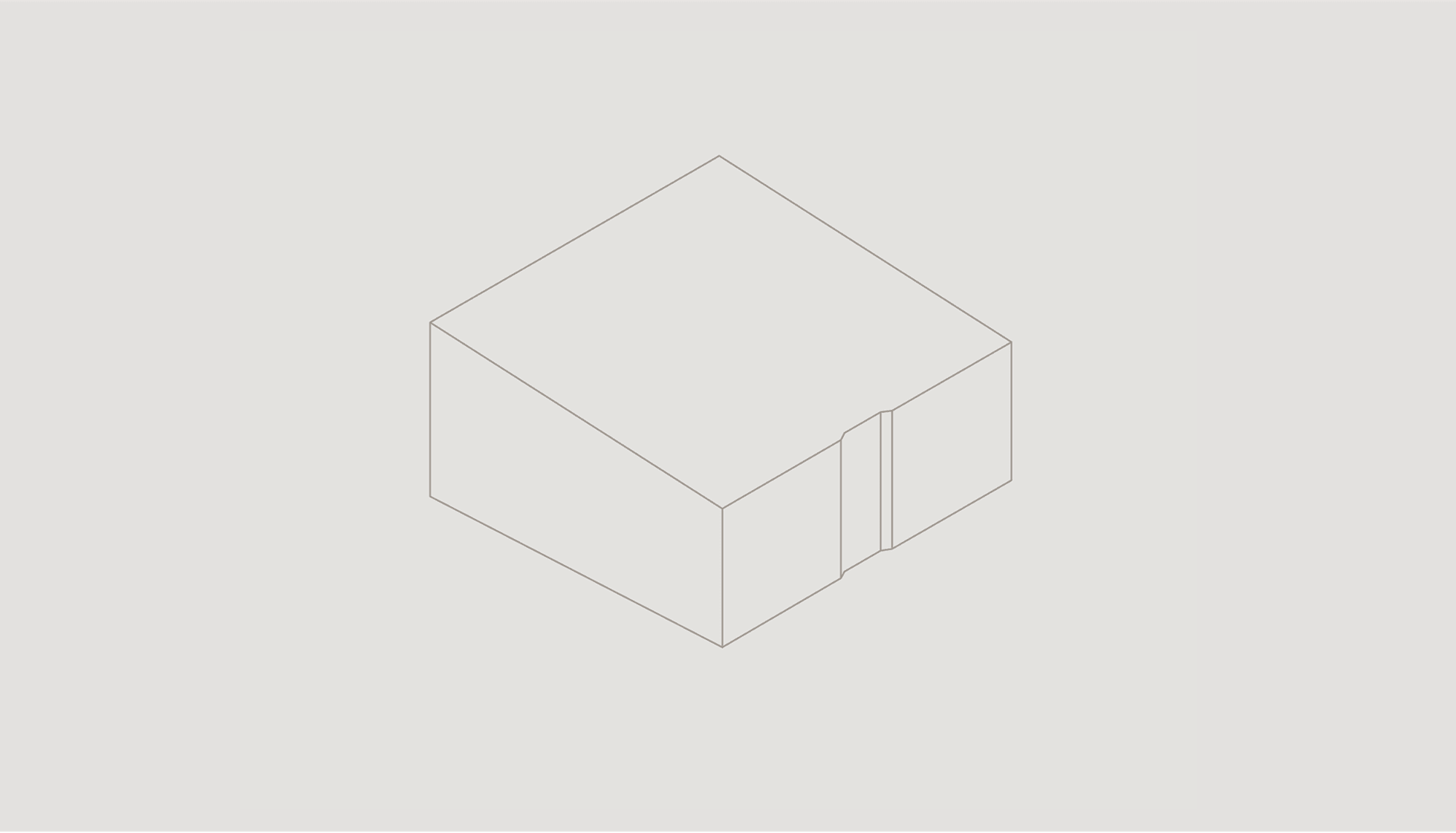
Produktlinie ABRAL
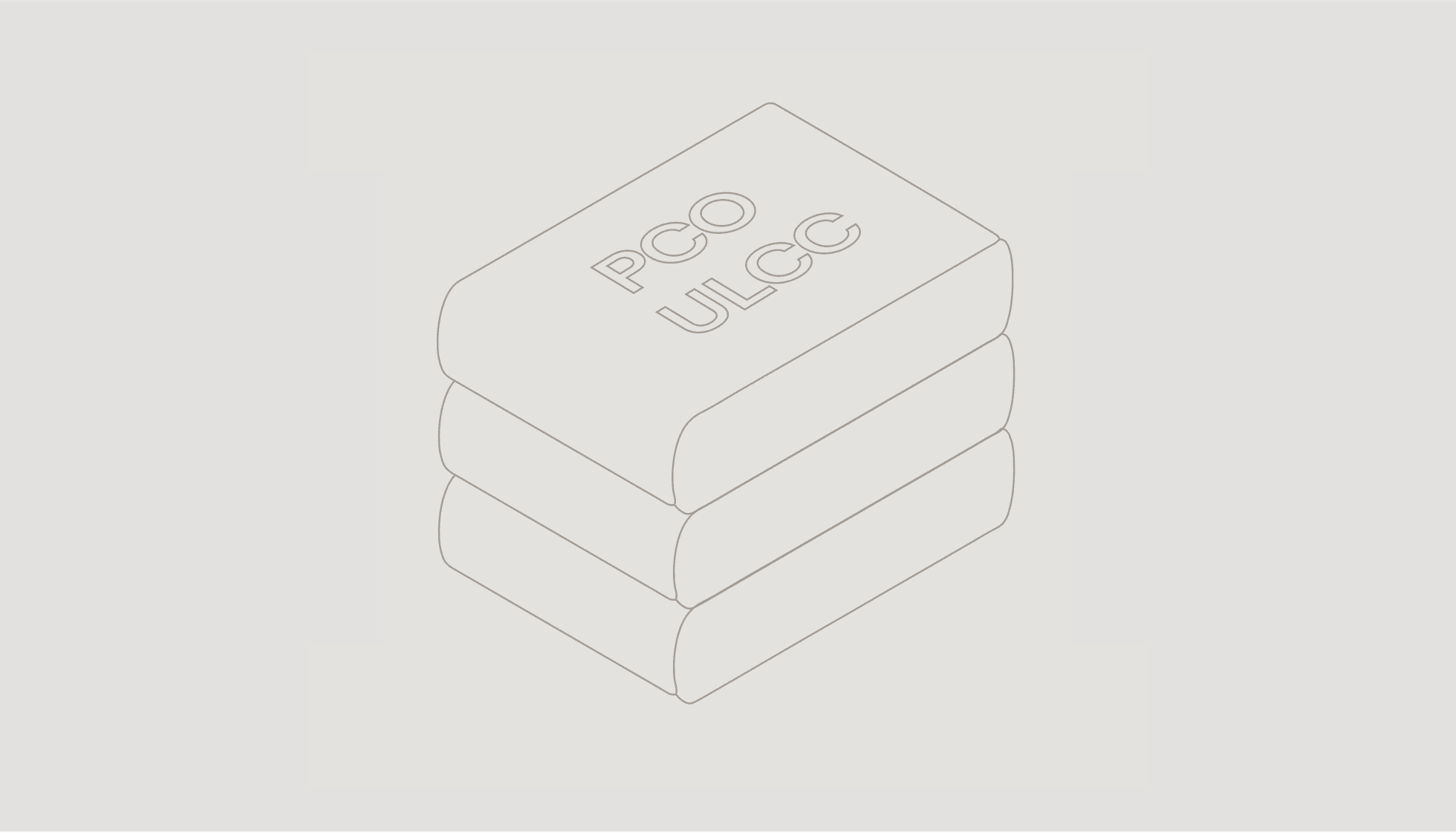
ULCC – Ultra-niedrigzementäre Feuerbetone
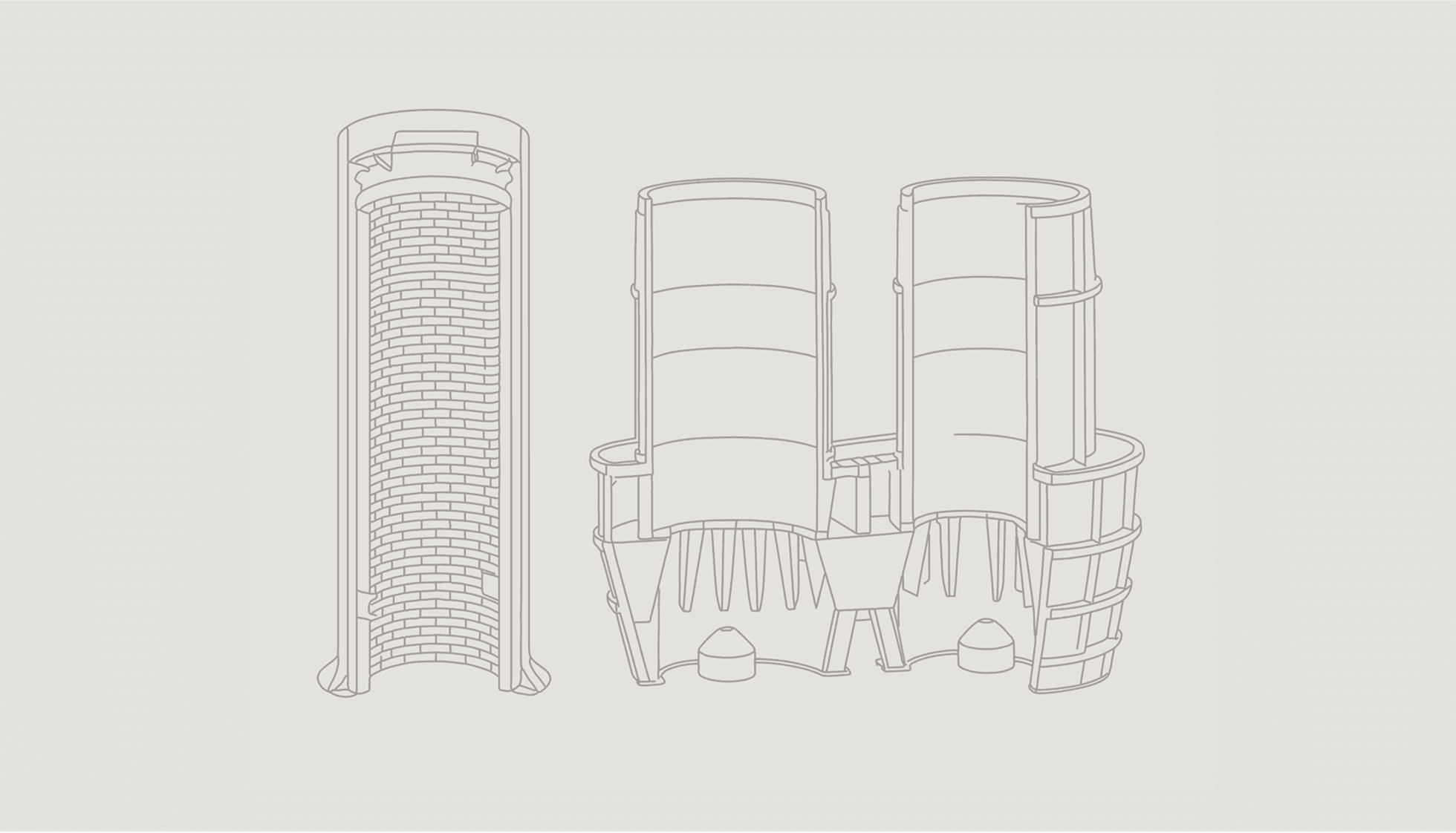
Bauaufsicht für Schachtöfen und Maerz-Öfen
Kontakt
Wählen Sie bitte die Option aus, die das Thema, das Sie mit uns besprechen möchten, am besten beschreibt. So können wir Ihre Anfrage an die richtige Person bei PCO weiterleiten.